La cadena de valor del calzado impulsa un proyecto de ley de estímulo al desarrollo troncal del sector. La intención es tender un puente de una década, un trayecto de desarrollo acelerado que en cinco años esté en condiciones de ofrecer por primera vez saldos exportables de mano de obra argentina, es decir, volúmenes significativos con precios y calidad internacional; y en diez años una cadena de valor totalmente integrada con insumos nacionales y que esté en condiciones de competir abiertamente con las grandes potencias productoras del sector.
La historia de la industria del calzado argentino tiene una larga tradición, no solo en zapatos y calzado informal, sino también en zapatillas. Empresas como Alpargatas y Gatic fueron las responsables de la llegada de las principales marcas internacionales al país, y con ello de la creación de todo un sector productivo que las abastecía de productos con la etiqueta “Hecho en Argentina”. Esas zapatillas incluso llegaron a ser muy valoradas en el exterior, como ciertos modelos creados por Gatic para Adidas en la década del '80.
De aquella experiencia industrial quedaron fábricas como Extreme Gear en Esteban Echeverría, Coopershoes en Las Flores, Alpargatas en Florencio Varela, Tecnosport en Luján y Paquetá en Chivilcoy, a las que se sumarían años más tarde las plantas de Puma en La Rioja, de Topper en Tucumán y de Grupo Dass en Misiones. la Argentina era fuerte en la fabricación de zapatillas, aunque esa fortaleza siempre dependió del contexto económico y, principalmente, de cómo se balanceaban las importaciones y exportaciones.
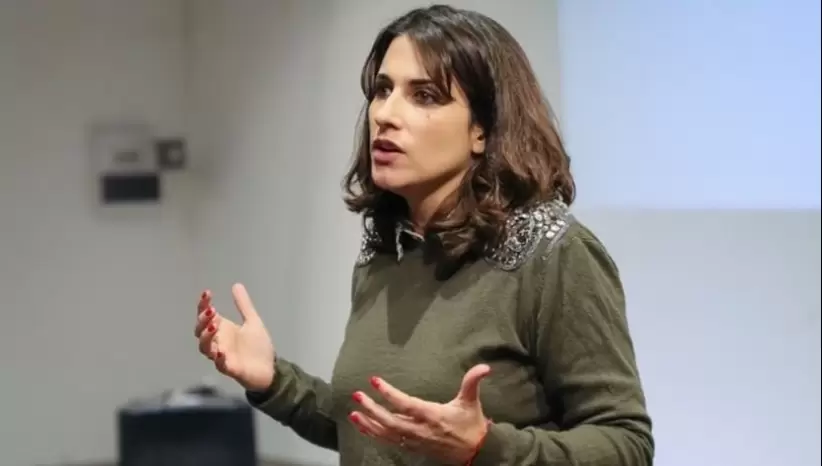
“De un día para otro, fuimos una de las ciudades con mayor desempleo de la provincia”, dice la diputada María Constanza Alonso (FdT) -chivilcoyana e impulsora del proyecto- sobre el momento en el que el gobierno de Mauricio Macri liberó las importaciones de zapatillas y productos deportivos. “Este proyecto viene a resolver la necesidad de no repetir la historia. No podemos abrir y cerrar, una y otra vez, como el mito de Sísifo: en el medio las empresas pierden capital y oportunidades comerciales, y los trabajadores pierden su calidad de vida, porque el trabajo es el gran ordenador de la sociedad”, agrega.
“La industria del calzado ha tenido ya al menos tres oleadas de cierre masivo de industrias y reapertura, ciclos de auge y decadencia, de quiebre generalizado impulsado por las exigencias de una competencia absolutamente desleal o de hiper-renta de trecho corto promovida por voluntad de la política de gobierno pero no de políticas públicas de largo plazo, conocidas por todos, claras, predecibles y no alterables por las preferencias de quien toma circunstancialmente el timón de gobierno en cada turno”, dice Juan Recce, titular de Bicontinentar, la ex Paquetá que Chivilcoy recuperó como referencia productiva del sector en la provincia.
El proyecto nace de la experiencia de las grandes fábricas de calzado deportivo de capital nacional. En 2015 había 10 que empleaban a casi 15.000 personas. A fines de 2019 quedaban 4 y daban trabajo a poco menos de 2.000 personas. En el sector del calzado tradicional pasó algo parecido: cientos de pequeños talleres que daban trabajo atomizado en distintos puntos del país se extinguieron. Con el cambio de las políticas públicas de producción algunas industrias reabrieron y otras no lograron recuperar el capital perdido en el proceso de cierre y no volvieron a abrir.
El proyecto es apoyado por prácticamente toda la cadena de valor, incluyendo al sindicato del calzado, a la cámara empresaria y a los dirigentes políticos y legisladores de las provincias y localidades donde hay industria del calzado. “El proyecto se fue puliendo con los aportes y las miradas de todos sectores”, dice Recce. “No es fácil construir un modelo que sea representativo de todos los intereses de máxima, pero logramos el mejor modelo de consenso, el más responsable, el que nos permite primero sobrevivir, luego volvernos más autónomos y finalmente transformar el sector”, agrega.
La Cámara de la Industria del Calzado destaca su sostenibilidad y sustentabilidad. “Apoyamos e impulsamos el proyecto porque incluye a toda la cadena del sector, e involucra innovación, tecnología e inversiones”, dice Horacio Moschetto, secretario de la Cámara. “Hoy el ensamble de componentes extranjeros tiene menos aporte de mano de obra y materias primas nacionales, y está previsto que con la ley eso aumente año tras año”.
Por ahora, no parece haber voces en contra. Contempla los intereses de los consumidores (abarata el precio final), de los trabajadores (promueve el blanqueo y la formalización de su situación), del fisco (genera empresas que luego tributan) y hasta de las marcas (si se integran los componentes locales, se evitan problemas de logística). “Si se cumplen los plazos y metas, en unos años la industria estaría en condiciones de competir con cualquiera, de generar dólares para el país en vez de consumirlos”, dice Alonso.
En la actualidad el mercado argentino de las zapatillas está compuesto por alrededor de 30 millones de pares anuales (en promedio, menos de un par por persona al año). Algunos llegan al país terminados y listos para vender, otros son fabricados a partir de componentes que también son importados. Y el resto es pura producción local. Aproximadamente 25.000 personas trabajan formalmente en la industria y otras 25.000 en la economía informal.
“La gran ausencia en la industria local es el abastecimiento nacional de bienes intermedios, con variedad y volumen y calidad global”, dice Recce. “La Argentina tiene todos los bienes de la naturaleza necesaria para producir calzados: cueros, hilados, polímeros de la industria petroquímica, y tiene la mano de obra y los equipamientos para la construcción del calzado; le faltan los bienes intermedios, la agregación de valor necesaria para que esos bienes de la naturaleza se transformen en los insumos que la construcción necesita. Nos falta variedad, complejidad, volumen en el segmento de proveedores”, agrega.
María José Fossati, directora General y CCO de John Foos, tuvo esa misma experiencia cuando la firma salió a buscar proveedores para su nueva línea sustentable JNFS.DOTS, confeccionada con materiales reciclados. Mientras que en el exterior ya se producen calzados hechos con materias primas recuperadas y reutilizadas (telas, caucho, plásticos y metales), en la Argentina se trataba de una experiencia casi inédita. “John Foos tiene la capacidad industrial para producir de principio a fin, pero conseguir materias primas que cumplan ciertos requisitos de sustentabilidad fue lo que nos llevó más tiempo”, afirma.
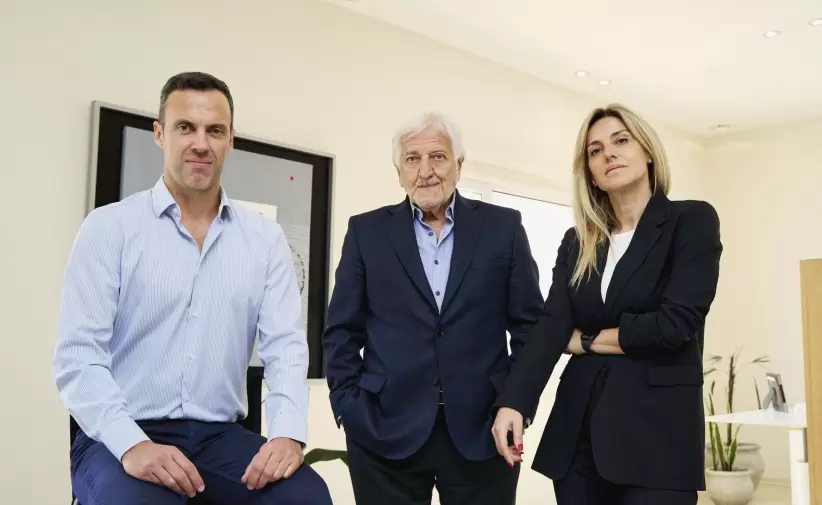
Las reglas del juego actuales fomentan el ensamble y la fabricación, y desalientan la importación de pares terminados. Y todas las marcas se adaptaron al entorno. Quien lleva cierta ventaja comparativa es Puma, la única marca deportiva que cuenta con una fábrica propia en La Rioja. “Puma produce el 80% de lo que se comercializa en el mercado local y contamos con un plan de inversión para ampliar la capacidad productiva a 4 millones de zapatillas para abastecer la demanda de los consumidores argentinos”, indican desde la firma.
Los impulsores del proyecto trabajan en instalar el tema y en destacar que terminará beneficiando a los consumidores: propone un cambio en el sistema de etiquetado, que incluya la fecha de fabricación de cada producto y que, a partir de ella, se establezca un plazo a partir del cual los productos deban venderse a precio de liquidación. Las expectativas son moderadas, pero optimistas. “Queremos dejar de consumir dólares en bienes intermedios, es decir, de consumo corriente, para aplicarlo a los bienes de capital”, dice Recce.